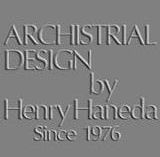
#archistrial, archistrial, ,knife ,cutlery knife, ERGONOMIC, ERGONOMICS, BIONOMIC, BIONOMICS, BIO DESIGN, CUTLERY , KNIFE, DESIGNER, HENRY HANEDA, ROD, RODS, FISHING, LURE, FLYFISHING, BLADE, BLADES , TOPS, ARCHISTRI, CHEF KNIFE, ORGANIC DESIGN, ERGONOMIC, BEST CHEF KNIFE, KNIFE MAKER, SEATTLE, TACOMA, BLADESMITH, CRAFTS, COMPOSITE , BORON, GRAPHITE MASTER, ART, DESIGN, DESIGNER, LEGEND, PHOTOGRAPHER, PHOTOGRAPH, PHOTO
NEWS BLOG 01/ June 2013~April 2014
BIONOMICS CUTLERY April 20 . 2014

BIONOMICS CUTLERY

BIONOMICS CUTLERY

BIONOMICS CUTLERY

BIONOMICS CUTLERY
Just before the mass production knives model went into the final stage.
いよいよ包丁の量産直前モデルは検討最終段階に入りました。バイオノミクス・コンセプトによる包丁シリーズは握りやすさを追求し、調理人への手,そして体全体への負担を大変軽減するため大きな期待がもたれています。鋼材はプロシェフからの希望が多い日本古来の手打ちの刃物鋼、また手入れが楽でエッジホールディング性能(刃持ち)に優れたVG10などを計画しています。
グリップ素材はペーパーストーン(リサイクル紙を使用し、カシューレジンで硬化した米国産素材)やウッドを予定しています。ウッドは2年に渡り激しいテストを行い良い結果の出た樹種を使用します。
BIONOMICS WOODEN GRIP Nov 21, ~ September 21 2013

ココボロのすばらしい色と木目、今まで見たことのないすばらしいものである。バットはオリーブグリーンで赤っぽいグリップ部を引き立てる。このオリーブ色の杢は非常にレアで今回のみ、素材はこれ1個しか入手出来ず。価格はスタンダードの$300UPです、グリップのカタチはさらに変化し、機械加工より手加工を多くして複雑な曲面を素材の欠けなく仕上げに成功。限定品。エングレービング無しでもすばらしいフィット感,滑りにくい形状で大変安定感があります。

ココボロのすばらしい色と木目、今まで見たことのないすばらしいものである。バットは黒檀のようなアフリカン・ブラックウッドでオレンジがかったグリップ部を引き立てる。価格はスタンダードの$300UPです、グリップのカタチはさらに変化し、機械加工より手加工を多くして複雑な曲面を素材の欠けなく仕上げに成功。限定品。エングレービング無しでもすばらしいフィット感,滑りにくい形状で大変安定感があります。木目は限定品で今回の特製品2本のうちの1本です。今後このグレードの素材の入手は非常に困難です。

グリップ前方下部側からの写真。以前の制作時よりフィンガーグルーブの深さが増し、握った状態でのフィットが向上した。

ココボロのすばらしい色と木目、今まで見たことのないすばらしいものである。バットはオリーブグリーンで赤っぽいグリップ部を引き立てる。このオリーブ色の杢は非常にレアで今回のみ、素材はこれ1個しか入手出来ず。価格はスタンダードの$300UPです、グリップのカタチはさらに変化し、機械加工より手加工を多くして複雑な曲面を素材の欠けなく仕上げに成功。限定品。エングレービング無しでもすばらしいフィット感,滑りにくい形状で大変安定感があります。
ついにウッドのグリップパーツも自社生産が可能になった。
フォルムはより理想的になり、問題だった加工中での突起部の切削中の欠損も解決された。参考写真はウッドグリップのバット部にアフリカン・ブラックウッドを使ったものを紹介しているが、このウッドは非常に固く、多くの加工時間を要し、受注生産のみ制作しています。通常品は従来通りのような組み合わせとなる。こういった最も困難な加工をクリアして来ると今になって色々な面で生産に余裕を感じる事が出来る。
Made in Tacomaだ!
Nov 21 : 木製グリップの製造は少しずつ量を増やしつつあり、多くの木を比較検討して来た。初期からメイン素材に使用して来たココボロは危惧種レベルⅡに指定され、現在は国際間での原木や製材品の取引が禁止された。価格は大きく上がり、いずれレベルⅠに指定され使用した完成品販売も国際取引が禁止される可能性がある。美しいだけでなく、耐水性、耐摩耗性、傷に強いなどメリットは多いが他に変わる素材も検討しなければならない。
製造者が実際に手にとって原材料を選び、今回超レアといえるココボロの珍しい木目、色のものを加工した。今まで見たことのないすばらしいものだった。また入手困難なハワイアンコアウッドのグリップも完成。画像を追加したのでご覧ください。
BIONOMICS 2000 GRIP September 18 2013
BIONOMICS 2000 GRIP PROJECT
BIONOMICS 2000 GRIP PROJECT は予定通り進んでいます。製作は多くの技術が必要で容易ではありませんでしたが、ひとつひとつクリアーして来ました。昨日17日にはウッドのフレームの外観の削りだしが終わりました。今日18日は左右のウッドの接着とバット部の二種のウッドの接合と成形です。いよいよ次ぎには完成をお見せ出来ますね。ここ迄非常に長い時間がかかりました。世界で最も経験のあるガン・グリップ製造のトップメーカーが当グリップの製造を中止した、曰く付きの取り扱いの困難な天然木の加工をマスターするのは本当に多くの事を経験し、必要な技術を獲得する事でありました。一つでもミスがあれば全てが駄目になってしまいます。最初は、米国の長い歴史の在る最高のメーカーが出来ないと断ったときの説明を聞いた時は、自力で作るのは容易ではないなと思いました。やってみると可成りの思考錯誤と工夫研究を要しました。良いものを作るとの約束は守らねばならず、早く仕上げることを焦り、しかし、拙速に走る事は許されず常にジレンマに悩まされました。本当に焦りを感じましたが、くじけなければ達成出来る事を実証する事の大切さを感じます。

BIONOMICS 2000インターナルフレームとグリップのフィッテイング

接合前の左右のウッド部品

薬指のあたる部分は深く彫られより握りやすさを増している。外注時には切削加工中にウッドの山の頂点が研削刃でチッピングを起こすのでアールを大きく取らざるを得なかった点は加工を工夫し解決した。その結果さらに握りやすくなった。

BIONOMICS 2000インターナルフレームとグリップのフィッテイング
BIONOMICS 2000 WOODEN GRIP September 05 2013

BIONOMICS 2000 GRIP バイオ2000の製造で最も問題だった木製のグリップ部品は、天然木での安定製造 が非常に困難な事から、外注先のメーカーは天然のウッドグリップ製造を中止し、替わりに樹脂含浸木材で樹脂含浸のウッドでのみ製造可能と言う残念な結果となりました。樹脂含浸ののウッドは石のよう固く、エングレービングの刃が滑るため実際の加工は非常に困難で理想的とは言えず、どうしても天然木での生産を可能とする方法を見つけるため自社内であらゆる試行錯誤を行ってきました。何年もの努力の結果が実り、現在必要な経験、工作機械の準備は全てそろい、いよいよ本格的に自社製造開始いたしました。機械のセッティングなどで最初は少量ですが、徐々に数を増やして行きます。板の木目を左右合わせて選び定寸法に切断、そしてタングステンの刃でフレームの入る部分を切削します。左右を合わせて接着後には、外形の成形へと進みます。今後、加工行程の要所写真を掲載して行きます。左の写真はフレーム受け部,右側面部の加工が終わったところです。
追伸:Sep. 08
昨日、最も重要なウッドの左右の板のフレームの入る部分の切削調整が出来あがり、左右合わせがぴたりと決まりました。 これで今後の流れが加速します。この加工のためにジグと工具を作り生産性が上がる工夫をするのが最も時間がかかりましがこれで一番の山を超えました。後は黙々と作業を続け、今迄に地道に蓄積した加工技術で仕上げられます。結果的に今回の生産では、技術の工夫と向上などでさらに物作りの巾が広がりました。
NEW WOODEN GRIP September
日本人の手のサイズを基準に製作した銘木シリーズのバイオノミクスオリジナル型のグリップです。フレームは希望によりフジ製の13ミリまたは15ミリアダプター径のものを製作します。いずれもシャフトは着脱式になります。



EXTENDED HANDLES FOR BIONOMICS 2000 GRIP July 10 2013

バイオ2000グリップの愛用者からの注文で製作したテーパー付きのアフリカン・ブラック4インチハンドルです。バットには極上の目の揃ったアンボイナバールを使用しました。

バイオ2000グリップ用のアフリカン・ブラックのインチエクステンデッド・ハンドルです。バットには珍しい二色の目のアンボイナバールを使用しました。金属部品は未接着の為,ご希望にあわせ4インチ以上にも可能です。グリップは完成在庫品であるため48時間以内の出荷が可能です。

バイオ2000グリッ プ用のアフリカン・ブラック4インチエクステンデッド・ハンドルです。バットには珍しい二色の目のアンボイナバールを使用しました。金属部品は未接着の為,ご希望にあわせ4インチ以上にも可能です。グリップは完成在庫品であるため48時間以内の出荷が可能です。

バイオ2000グリップの愛用者からの注文で製作したテーパー付きのアフリカン・ブラック4インチハンドルです。バットには極上の目の揃ったアンボイナバールを使用しました。
日本のバイオノミクス2000グリップの愛用者からの特別注文で,アフリカン・ブラックウッドのエクステンション・ハンドル4インチを製作いたしました。バット部にはアンボイナのバールを使用し、緩やかなテーパーでバット側がやや太くなるようにし、握りの部分を出来るだけ長く取るデザインとし、握りやすさを追求。
今回はアフリカン・ブラック素材の予備があるため2本を完成在庫としました。また別の方からの特注で、アンボイナの二色の混ざった4インチと6インチのハンドルも製作。
素晴らしいレアウッドのハンドルの希望者がますます増えてきました。グリップの完成在庫品は金属部の接着をしていない物もあり、金属部の長さを希望に合わせ加工いたします。金属部はパイプからの加工したストレートと,無垢のバーストックからテーパー状に削りだしたインテグラルタイプがあります。
他にメープルやオリーブウッドなどの完成在庫品もあります。4インチから最長12インチまで製作可能です。
I had a very gratifying visit this morning to a 3D printer lab in Seattle, because it validated an idea I have had for a long time about the 3D printing process.
It was an eye opening experience that convinced me that 3D printing would revolutionize the entire goods manufacturing industry. In the past, people whose hands are either smaller or bigger than the norm were ignored in the mass production process, because it is too costly to tailor make products to suit them.
However, 3D printing now makes it possible to customize products for these people at nearly the same cost. Furthermore, it can significantly reduce product development time, prototyping and testing prior to final production. The most notable thing is that by using 3D printing, it's possible to get 100% customer satisfaction every time.

"CATCH AND RELEASE" HENRY HANEDA PHOTOGRAPY B2 GALLERY June 18 2013



My photo exhibit came last week to its successful completion. I am grateful to the support given to me by those who care for my work.
It was a tremendously uplifting experience.
And also I would like to announce that I will be showcasing my works next month at the newly opened gallery on 6th Avenue in Tacoma.